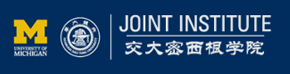
Student Projects
VG100
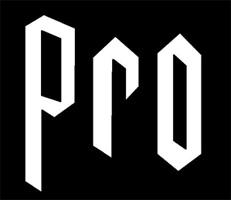
Autonomous Parcel Sorting Device
Instructors: Dr. Mian Li, Dr. Irene Wei
Team Members: Haolin Cen, Yinghui He, Yuchen Wang, Yuzhuo Liu, Zhaoyuan Liang
Project Video
Team Members
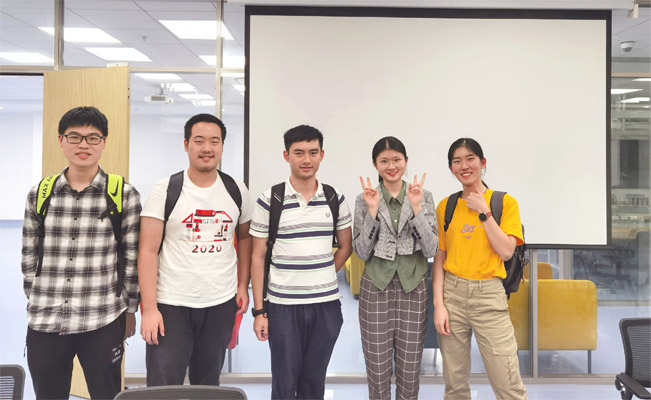
Team Members:
Haolin Cen, Yinghui He, Yuchen Wang, Yuzhuo Liu, Zhaoyuan Liang
Instructors:
Dr. Mian Li, Dr. Irene Wei
Project Description
Problem
Multiple solutions have been introduced before, but numerous drawbacks exist.
Concept Generation
Design Description
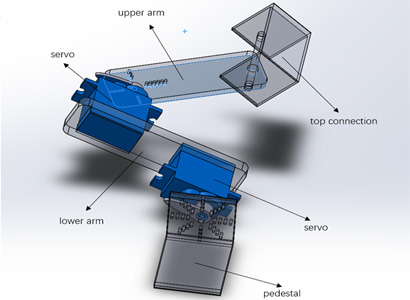
Modeling and Analysis
The unloading function is achieved by the structure illustrated below, which consists of a unloading panel and a mechanical arm.

Validation
*Measured weight: the weight measured by our device; Actual weight: the data obtained from a precise electronic scale.
Actual route: the route followed by our device in the test; Expected route: the expected route determined by the actual weight of the parcel.
The measured weights are less than the actual values, which resulted in inaccurate route determination. By analysis, such error is caused by the systematic error of the weight sensors, and deficiency in the weighing program. Further optimization is needed for the weighing program.
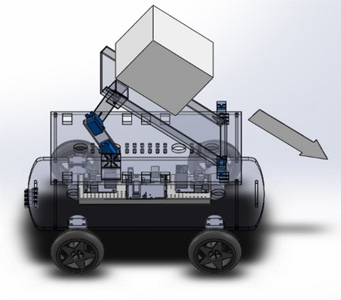
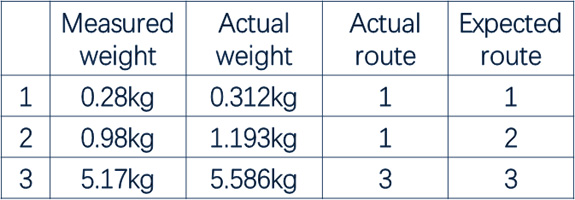
Conclusion
The general technical outcomes are demonstrated below:
- The device performs route tracking according to the weight detected.
- The device moves between terminals under the program uploaded.
- The device can unload the parcels autonomously after each arrival at an individual terminal.
- The device reaches designated terminals within relatively short time.
Acknowledgement
Teaching Assistants [Fubo Qi, Hanyang Feng, Sheng Qiao, Xiaoxuan Wang] for VG100 at UM-SJTU Joint Institute.
More project information, please contact: heyinghui@sjtu.edu.cn