Student Projects
VE/VM450
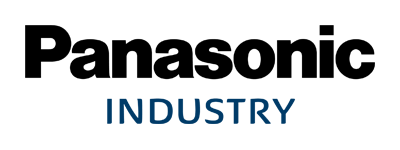
Portable Cargo Volume Measurement System
Sponsor: Pengcheng Ma, Jingjing Zhang, Zhuosi Zhang, Panasonic
Team Members: Songqian Li, Kun Huang, Chen Peng, Yuyi Qu, Yilun Zhu
Instructor: Prof. Shouhang Bo
Project Video
Team Members
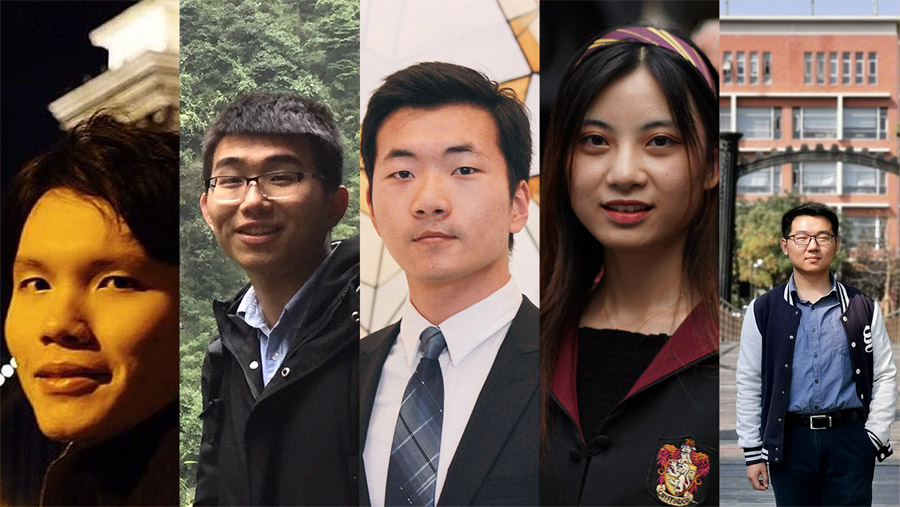
Team Members:
Songqian Li
Kun Huang
Chen Peng
Yuyi Qu
Yilun Zhu
Instructor:
Prof. Shouhang Bo
Project Description
Problem Statement
In this e-market era, cargo volume measurement is critical to logistic industry. Manual measurement is slow, error-prone and tedious. This project aims to build a portable system that gets the dimensions of cargoes with only one-click, at the same time with better accuracy and efficiency.
Fig. 1 Traditional Manual Measurement(L) & One-click Measurement(R)
Concept Generation
The system takes the picture as input and output the measures on the screen. It first process the depth image, then convert it to 3D. By finding the planes and corners, dimensions and volume can be evaluated. The detailed description of our project is shown in figure 2.
Fig. 2 Concept Diagram
Design Description
The design contains 4 subsystems:
- The images taken by user is transmitted to the console through WLAN.
- Next, the raw image is processed by pixel-wise bias elimination and denoised by Bilateral Filter[1].
- Then, convert 2D image into 3D Point Cloud and fit planes using RANSAC algorithm[2].
- After going through a well-designed 2D-3D processing pipeline to find corners, dimension measures are available.
Finally, the results will be shown on the GUI of the console.
Fig.3 The whole set-up system
Modeling and Analysis
A MATLAB model is built to perform dimension and volume measurement. It firstly reads the image taken by users. Then perform the sophisticated 2D-3D processing pipeline described above. The following graph shows the processed output: fitted planes and corners.
Fig. 4 3D model reconstructed from image
Validation
Validation Process:
Key performance are the accuracy and the speed of the algorithm. We first measure the dimension of cargoes manually. Then take photos of them and run our system.
By comparing the result, we get accuracy. Using tic,toc function in MATLAB, running time is available.
Some other requirements are verified by our design.
Validation Results:
According to validation part, most specifications can be met.
√ Portable, User-friendly
√ Volume Accuracy >=99%
√ Cost <= 3000RMB
• Running time <= 500 ms
• Dimensions Relative Error < 3‰
√ means having been verified and · means to be determined.
Conclusion
Our project shows that vision-based dimension measurement provides a good alternative to manual process. The biggest challenge arises from the imprecise raw data captured by ToF camera. We therefore developed various methods to compensate for systematic error and reached robust and precise measurement.
Acknowledgement
Sponsor: Pengcheng Ma, Jingjing Zhang, Zhuosi Zhang from Panasonic
Instructor: Prof. Shouhang Bo and from UM-SJTU Joint Institute
Reference
[1] Aurich, V., Weule, J.: Non-linear Gaussian filters performing edge preserving diffusion. In: Proceed. 17. DAGM-Symposium (1995)
[2] Fischler, Martin A., and Robert C. Bolles. “Random sample consensus: a paradigm for model fitting with applications to image analysis and automated cartography.” Communications of the ACM 24.6 (1981)