Student Projects
VE/VM450
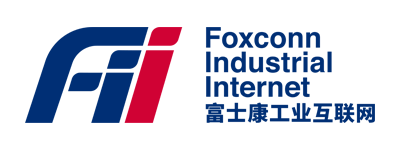
Virtual Measurement based on Manufacturing Data for the Injection Molding Process
Sponsor: Baoyang Jiang, Fei Liang, FII, Mian Li
Team Members: Zeyu Zhang, Xucheng Ma, Fengyu Zhu, Kexin Weng, Jinru Li
Instructor: Prof. Chong Han
Project Video
Team Members
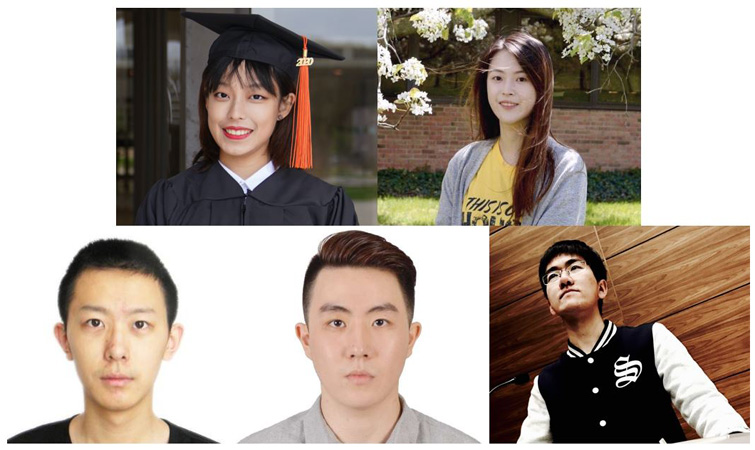
Team Members:
Zeyu Zhang
Xucheng Ma
Fengyu Zhu
Kexin Weng
Jinru Li
Instructor:
Prof. Chong Han
Project Description
Problem Statement
Injection molding is one of the most widely used techniques in the manufacturing process. Most electrical products we see in daily life have parts made with injection molding, phone cases, airpods cases. Injection molding process includes the steps of heating, injection, pressure holding, cooling, and product take out.
Although machines can do a much better job than human handcrafts, it also has limitations. Even when a machine is operating under the same condition and parameters, the product can have slight differences. When the difference is too large, it becomes a quality issue.
Fig. 1 Injection molding process [1]
Concept Generation
Throughout the production process, temperature, pressure and injection progress are monitored and recorded. What we want to predict is the dimension of the final product.
The first concept we generated was by using the multiple linear regression model. The second concept we generated was by using the Artificial Neural Network model to analyze the relationship between output size and input features. The third concept we generated was by using LSTM to analyze the time series data of sensors directly.
Design Description
The virtual measurement solution implemented all three methods to explore all possible solutions in this field. The solution has the following function decomposition.
Fig.2 Solution design description
Fig.3 ANN model design
Fig.4 LSTM model design [2]
Modeling and Analysis
Although it requires long training time and also heavy data pre-processing work, Neural Network is expected to yield best model accuracy, so we chose it as our primary method and other two as baseline methods. LSTM method use time series data directly, but it needs long training time. Linear regression method has best model interpretability since we can analyze statistics like R-squared and F-score, but it provide relatively low accuracy.
Validation
Validation Process:
The engineering specifications of our project can be classified into three categories: model performance metrics (accuracy, error) calculated based on the test dataset, training cost (time, #datapoints) measured during training, and model interpretation statistics (R-squared) analyzed after training the model.
Validation Results:
Results are summarized in the table:
ESs | NN | LR | LSTM |
---|---|---|---|
Accuracy > 85% | 85.6% | – | 83.2% |
Error < 5% | 0.05% | 0.4% | 0.1% |
#datapoint for training [500, 2000] | 1128 | 2419 | 1936 |
Training time < 15min | 10s | <5s | 12min |
R^2 > 0.7 | – | 0.9 | – |
MSE < 0.1 | 0.0012 | 0.02 | 0.0025 |
Conclusion
The virtual measurement solution utilized sensor data monitoring manufacturing process. With low prediction errors, defect parts can be successfully detected without physical measurement, thus increasing industrial efficiency.
Acknowledgement
Sponsor: Baoyang Jiang, Fei Liang from FII
Professor: Chong Han, Mian Li from UM-SJTU Joint Institute
Reference
[1]http://labs.seas.wustl.edu/bme/Wang/index.html
[2] Nagorny, Pierre, et al. “Quality prediction in injection molding.”