Student Projects
VE/VM450
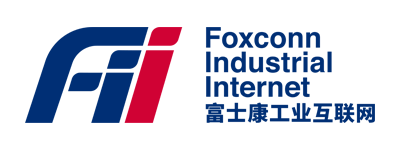
Virtual Quality Inspection in Sheet Metal Forming Processes
Sponsor: Baoyang Jiang, Peng Xu, Foxconn Industrial Internet
Team Members: Minjia Qian, Zhuzhu Wang, Youwen Zhu, Xiwen Chen, Qihong Liu
Instructor: Prof. Chong Han
Project Video
Team Members
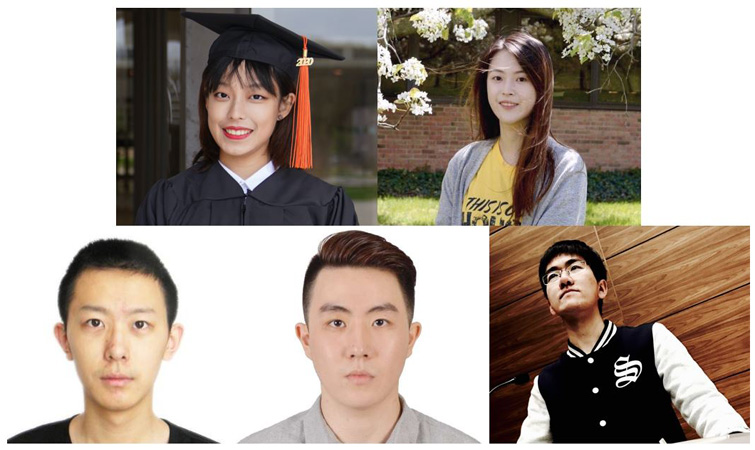
Team Members:
Zeyu Zhang
Xucheng Ma
Fengyu Zhu
Kexin Weng
Jinru Li
Instructor:
Prof. Chong Han
Project Description
Problem Statement
Sheet metal forming is one of the most important technologies in the manufacturing industry. However, during manufacturing, the errors in the press brake are invisible and hard to identify, which may lead to huge loss to the company. So our object is to develop a virtual quality inspection tool that detects quality issues by integrating sensing signals.
Fig. 1 Press Brake1 [1]
Concept Generation
Segmentation: One way to segment the signal is to use the findchangepts function in matlab. It gives the index at which the mean of x changes most significantly. Another way is to simply select a constant number of data points in the middle of the signal. It may not be as precise as the previous method, but it simplifies the system and saves time.
Denoising: Both Garbor transform and the wavelet transform helps reflect frequency and time behavior of the signals.
Training: We have tried different models in this part, such as envelope line, linear regression, SVM, and LSTM. We focus on envelope line. Since abnormalities happened in mechanical system will cause a sudden change in sensor signals, envelope line is an efficient tool to detect abnormal signals.
Design Description
With the concept generation & selection process, we finally combine the findchangept method in segmentation, wavelet transformation in denoising, envelope detection in training to a complete system. Figure 2 indicates how the subsystems interact and fit together. Part of the normal data (without extra particles in the raw metal materials) will be used as learning data for finding boundaries by envelope detection. The rest including normal and abnormal ones will be used to test the efficiency and effect of our system. We segment the first learning data as the reference signal (s_ref) to align the following signals. Then they are denoised in order to be smooth. At last, learning data will be used to find boundaries while the testing data will be labelled with the learnt model to evaluate it.
Fig.2 Layout for Conceptions
User Interface
A graphical user interface is designed to better visualize the method and predicted result. It features demostration, testing and recommendation functions.
Fig.3 User Interface
Validation
To test our algorithms, we use 90% of the data without error as the training set to first generate the envelope boundary. The remaining 10%, together with all the data labeled with error, form the test sets. This is to ensure that in the test sets, the quantity of data with error and data without error are compatible. For each test, the processing time and memory usage are recorded; and the accuracy is calculated by counting false predictions. Finally, the accuracy, processing time, and memory usage are compared to the engineering specifications to verify our algorithm. Table 1 below summarizes our specifications and validation results.
Table 1 Specification analysis
Conclusion
In conclusion, our project is to develop a virtual quality inspection tool for the sheet metal forming process. For detailed project design, we divide it into five steps: segmentation, alignment, denoising, threshold determination, and user interface. Up to now, we still have some potential problems, including unstable performance and non-intuitive threshold setting. For the future improvement, we would like to try the Neural Network method, which behaves more stably given more data.
Acknowledgement
Sponsor: Baoyang Jiang, Peng Xu from Foxconn Industrial Internet
Chong Han from UM-SJTU Joint Institute
Reference
[1] https://www.custompartnet.com/wu/images/sheet-metal/press-brake.png