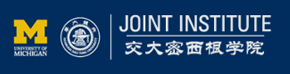
Student Projects
VE/VM450
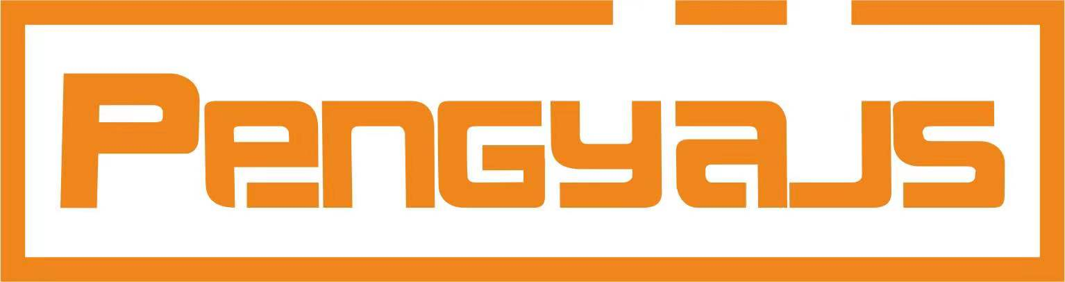
Intelligent Data Management Platform
Instructors: Prof. Mingjian Li
Team Members: Rong Tao, Rui Ding, Chao Xu, Yihao Zhang, Zhenhao Gu
Project Video
Team Members
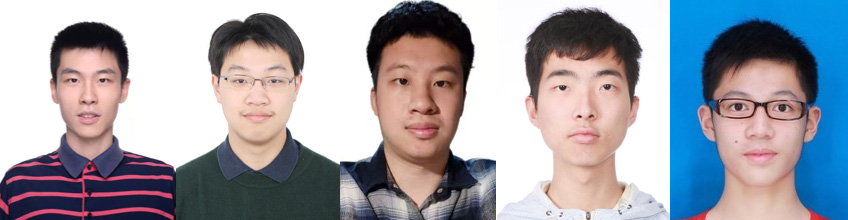
Team Members:
Rong Tao, Rui Ding, Chao Xu, Yihao Zhang, Zhenhao Gu
Instructors:
Prof. Mingjian Li
Project Description
Problem Statement
Our sponsor Pengya faces great challenges in the transition from traditional manufacturing to intelligent manufacturing. Due to the difficulty of data transmission, they lack database for recording sensor data and also an efficient visualization system to monitor their manufacturing devices. This project is aimed to build a system to monitor components of assembly line with database and visualization.
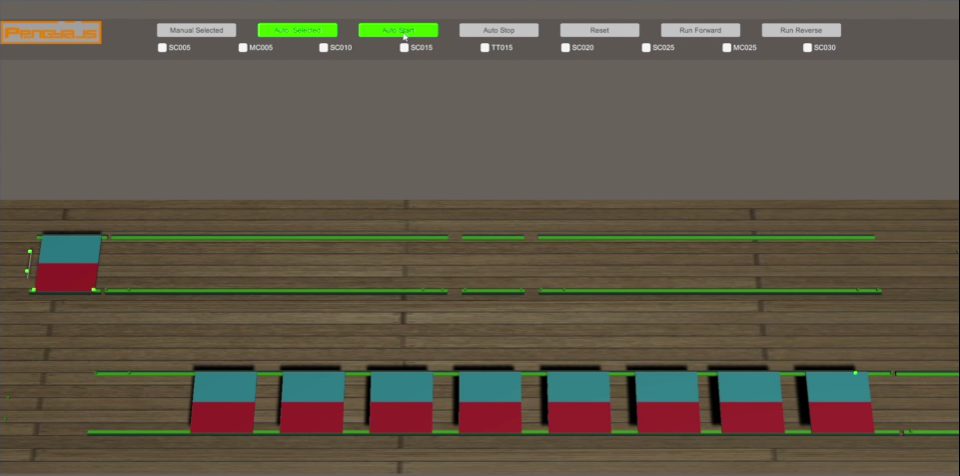
Concept Generation
The function of our intelligent data management platform can be decomposed into two parts, data storage and assembly line visualization. For database part, we also required the data format to be automatically optimized, which serves as a sub-function under the branch of data storage. For production visualization part, the first priority is to simulate the real-time behavior of original assembly line according to received data. It is also worth considering how to better present the whole assembly line to users.
Fig. 1 Simulation of Factory Assembly Line
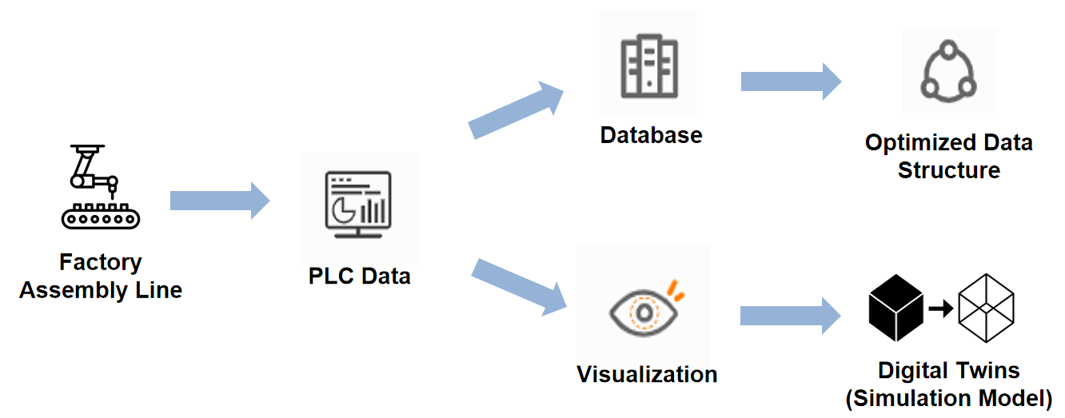
Fig. 2 Detailed structure function
Design Description
For data storage, we first established a channel in computer to connect data source and database. Then we load data into the database, and apply an optimization program to compress the database size. The database is designed to clear every 24 days, so that its size will be limited to 1GB. For visualization part, we established a 3D model, which can synchronize the working condition of original assembly line. After you click it, the component name of assembly line will appear and real-time data of sensors will also appear and be updated on top-left cornor of user’s interface.
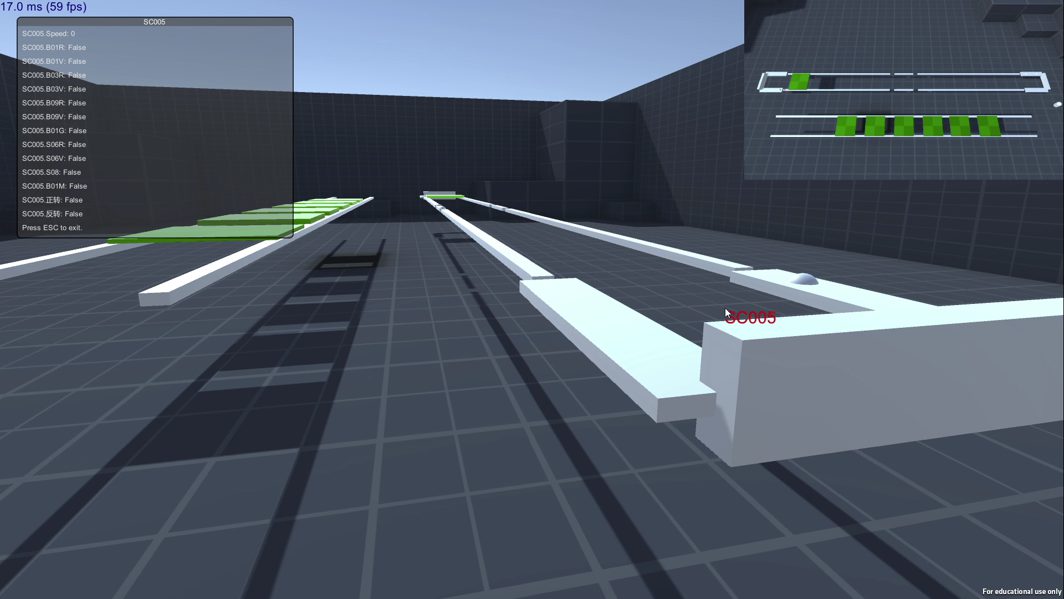
Fig.3 Digital Twin of Simulated Assembly Line
Modeling and Analysis
The modeling is mostly related to visualization part. We established a virtual 1:1 assembly line model (i.e. digital twin) as the original assembly line. After that, we connect real-time data collected from the assembly line to the digital twin. Based on the data collected, the digital twin can simulate the working condition of the original assembly line. Our model is well-synchronized with the original model and the simulation is precise.
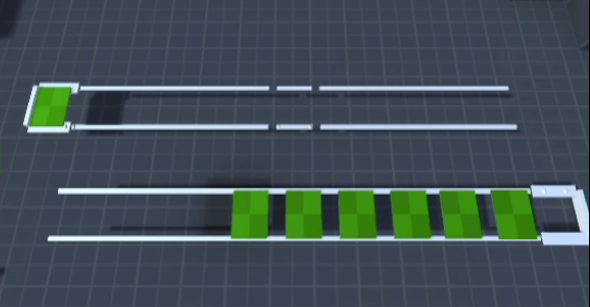
Fig. 4 Synchronous Behavior of Digital Twin
Validation
Validation Process:
We first run the simulated factory assembly line provided by sponsor and our own digital twin animation at the same time. Latency of data is measured by calculating the time difference of value changes in the sensor and database. Database size can be evaluated by checking the size of data file. Running memory cost for each components of project can be traced by monitor in Unity. FPS of animation can also be displayed by built-in function of Unity. Total cost of the project is 0, since we used free softwares throughout the project.
Validation Results:
According to validation part, all the specifications can be met.
√ Latency of Data < 1000ms
√ Database size < 1GB
√ Running memory cost <1GB √ FPS of Animation > 30fps
√ 3D Visualization
√ Initial Investment < 1000RMB
We first run the simulated factory assembly line provided by sponsor and our own digital twin animation at the same time. Latency of data is measured by calculating the time difference of value changes in the sensor and database. Database size can be evaluated by checking the size of data file. Running memory cost for each components of project can be traced by monitor in Unity. FPS of animation can also be displayed by built-in function of Unity. Total cost of the project is 0, since we used free softwares throughout the project.
Validation Results:
According to validation part, all the specifications can be met.
√ Latency of Data < 1000ms
√ Database size < 1GB
√ Running memory cost <1GB √ FPS of Animation > 30fps
√ 3D Visualization
√ Initial Investment < 1000RMB
√ means this specification has been verified.
Conclusion
Our intelligent data management platform can be used for supporting Pengya Intelligent Company monitor their manufacturing assembly line. They can use the system to inspect real-time parameters and trace the historical working records of assembly line. The key to achieve this goal is to (1) establish connection between data source and database, (2) reduce the latency in 3D digital twin.
Acknowledgement
Sponsor: Pengya Intelligent Co.
Mingjian Li from UM-SJTU Joint Institute
Chengbin Ma, Chong Han and Jigang Wu from UM-SJTU Joint Institute
Mingjian Li from UM-SJTU Joint Institute
Chengbin Ma, Chong Han and Jigang Wu from UM-SJTU Joint Institute
Reference
UM-SJTU JOINT INSTITUTE