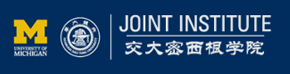
Student Projects
VE/VM450
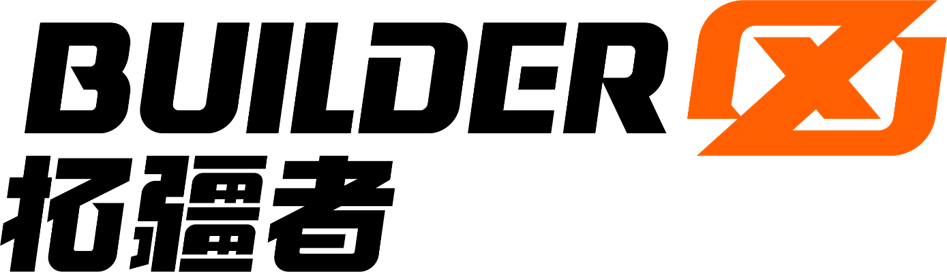
Prototype of Tower Crane Remote Control
Instructors: Dr. Mingjian Li
Team Members: Kaiwen Guan, Lap Chai LAI, Zhendong Liu, Yuhao Wu, Yihua Zhou
Project Video
Team Members
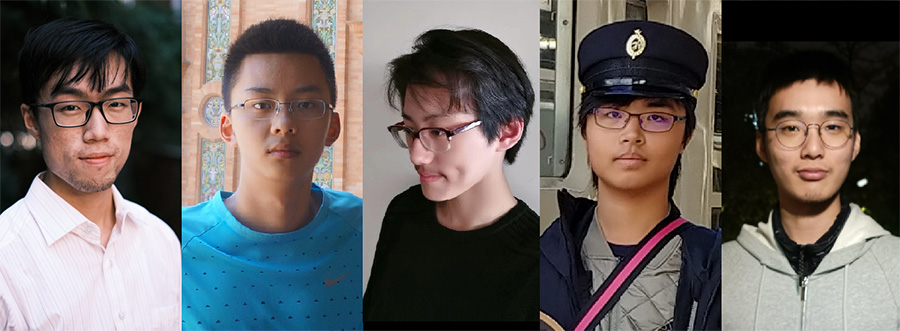
Team Members:
Kaiwen Guan, Lap Chai LAI, Zhendong Liu, Yuhao Wu, Yihua Zhou
Instructors:
Dr. Mingjian Li
Project Description
Problem Statement
Manual operation contribute to a considerable portion (up to 13%) of tower crane accidents around the globe. Also, the growing need for efficient construction calls for an increase in the efficiency of tower crane operation. Both safety and economic considerations creates the need for the development of unmanned remote tower crane. To achieve this, the stability of the tower crane hook is very important.
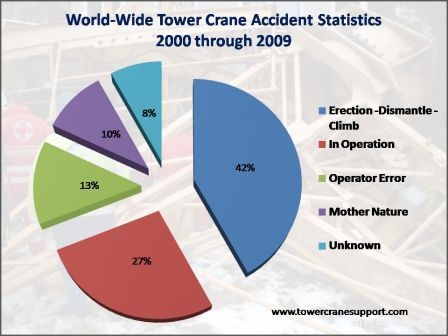
Fig. 1 portion of operating error in tower crane accidents [1]
Concept Generation
The design problem can be divided into three relatively independent parts.
One, we need to build a tower crane model, which is about 2 meters high from scratch. To validate the effectiveness of control strategy, we need to make sure that the model displays similar kinematic characteristics.
Two, a positioning method that enables us to get the coordination of the hook accurately and quickly is needed, as it provides information for motion control.
Three and finally, a control algorithm need to be developed based on the information gathered from the positioning system.
One, we need to build a tower crane model, which is about 2 meters high from scratch. To validate the effectiveness of control strategy, we need to make sure that the model displays similar kinematic characteristics.
Two, a positioning method that enables us to get the coordination of the hook accurately and quickly is needed, as it provides information for motion control.
Three and finally, a control algorithm need to be developed based on the information gathered from the positioning system.
Design Description
The detailed design include a tower crane model, with hook positioning detection using image recognition based on a camera mounted on the tower crane jib. For the control strategy, we chooses delayed feedback control.
The tower crane model is made primarily with aluminum extrusion beams and laser-cut aluminum plates. The height is 2 meters with a jib span of 1 meter. A gear system and two pulley systems facilitates the rotation and linear motion of the crane hook.
The tower crane model is made primarily with aluminum extrusion beams and laser-cut aluminum plates. The height is 2 meters with a jib span of 1 meter. A gear system and two pulley systems facilitates the rotation and linear motion of the crane hook.
Image recognition is chosen to determine the position of the crane hook. We put a red indicator on the top surface of the hook to make it easier to capture. After determining the position and velocity, we can use delayed feedback control to stabilize the hook position.
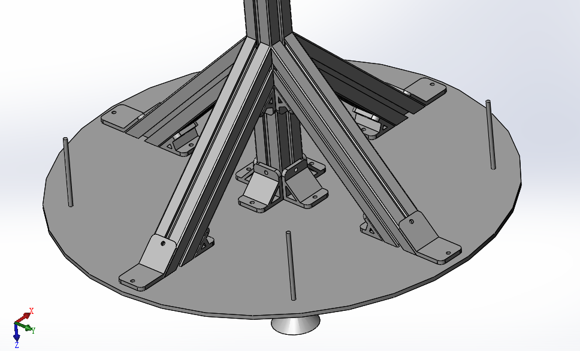
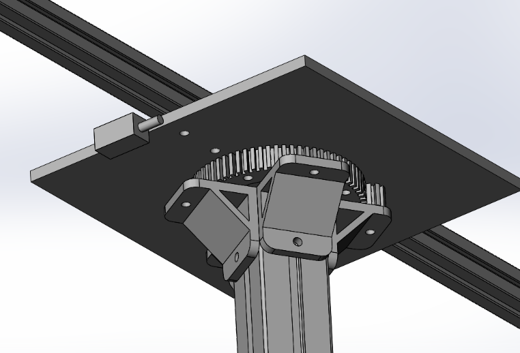
Fig. 2 The base and the top of the crane
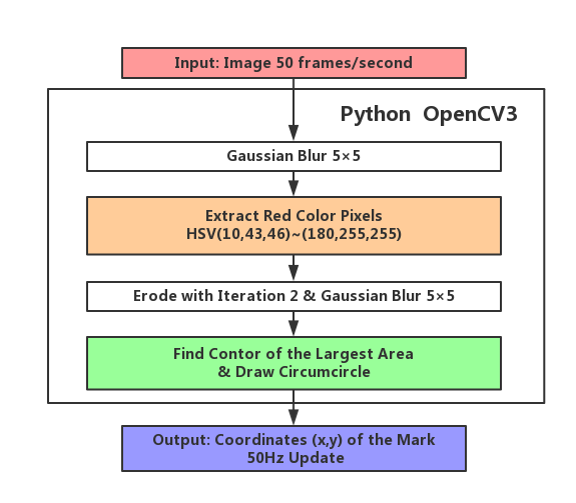
Fig. 3 image recognition algorithm
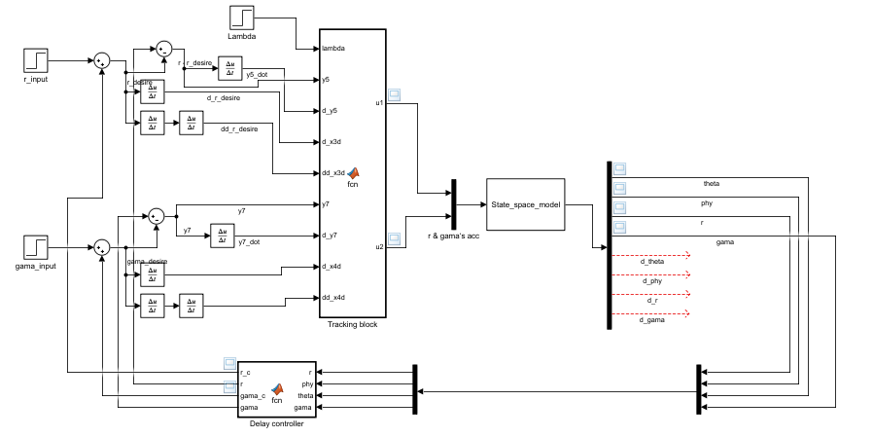
Fig. 4 block diagram of the controller
Validation
Validation Plan:
After manufacturing process, the tower crane model is finished, and some simple experiments can be carried out to test the stiffness of the crane model.
Validation Results:
√ Jib tip deformation <= 30 mm √ Tower top deformation <= 10 mm √ rotation speed = 7 rpm √ cart speed = 0.2 m/s · swinging amplitude <= 20’ · settling time <= 10 s · max overshoot < 10% · steady state error < 1° √ means having been verified and · means to be determined.
After manufacturing process, the tower crane model is finished, and some simple experiments can be carried out to test the stiffness of the crane model.
Validation Results:
√ Jib tip deformation <= 30 mm √ Tower top deformation <= 10 mm √ rotation speed = 7 rpm √ cart speed = 0.2 m/s · swinging amplitude <= 20’ · settling time <= 10 s · max overshoot < 10% · steady state error < 1° √ means having been verified and · means to be determined.
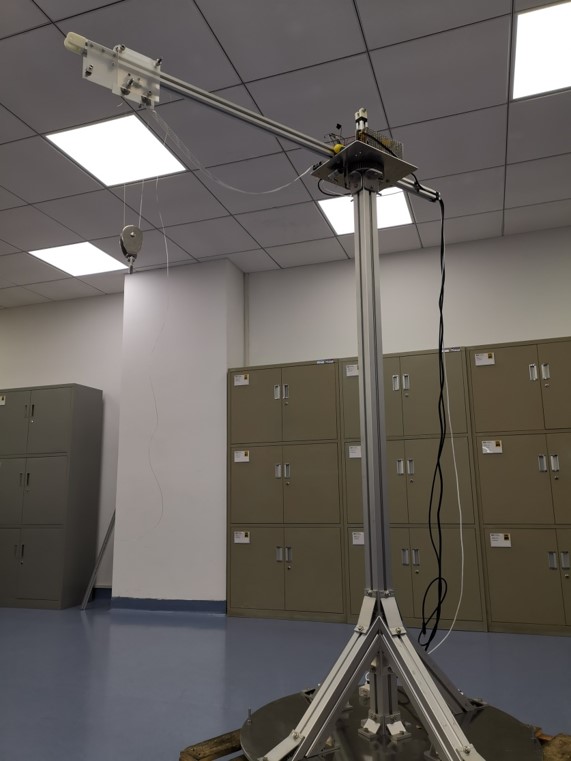
Fig. 5 The tower crane model
Conclusion
Remote controlling tower crane is achievable from the model built. Image recognition can be applied to identity the position of the crane hook under motion. The hook swinging amplitude can be reduced in a short time with a well-developed delayed feedback control algorithm.
Acknowledgement
Sponsor: Shaolong Sui from BuilderX
Instructor: Mingjian Li from UM-SJTU Joint Institute,
Instructor: Mingjian Li from UM-SJTU Joint Institute,
UM-SJTU JOINT INSTITUTE